Cooling Data Centers Is Costing Our Planet
The booming global market for more data centers will require enormous amounts of energy. Sustainable motors will be the key to meeting this demand.
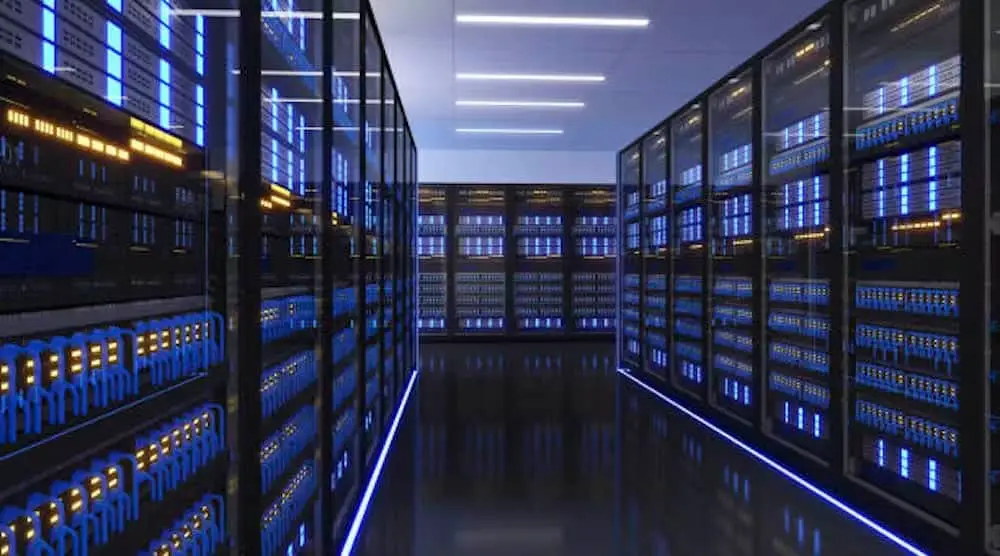
By JUSTIN SCOTT, Applications Engineer, Infinitum
Data centers have become increasingly critical to the world economy. As computing demands rise due to business reliance on cloud computing, the Internet of Things (IoT), AI innovations and Industry 4.0, more data is being generated along with the growing need to capture, store, evaluate and retrieve it. In the U.S alone, the data center market is projected to reach $69 billion by 2024.
And the more we rely on these capabilities, the more energy we require to support our computing needs.
In the U.S., data center energy consumption is expected to double, reaching 35 gigawatts (GW) by 2030, up from 17 GW in 2022. Additionally, with projections stating that by 2030 information and communications technology (ICT) will account for up to 20% of global energy usage, it’s evident that the growing demand for data center computing is becoming a pressing sustainability concern.
While demand is a major factor in energy consumption, higher outdoor temperatures can also play a role.
As external temperatures rise, data center facilities must “work harder” to maintain the required level of cooling. Liquid cooling, air handling units that can leverage free cooling and economizers, as well as precision cooling, are the types of innovative solutions that can increase the energy efficiency of data centers. In addition, HVAC equipment manufacturers are prioritizing sustainable, power-dense equipment that can handle higher levels of heat, while keeping data centers operating at lower temperatures.
Currently, 40% of the energy in data centers is consumed by motors that power cooling equipment, such as fans, pumps, and compressors. A typical data center employs an average of 500 electric motors to drive HVAC systems alone. Many of the motors powering today’s data centers are heavy and inefficient.
New advancements in motor designs that replace traditional heavy iron core stators with innovative materials, such as PCBs, have led to motors that are smaller, lighter, more efficient and power-dense. Some motors can also be precisely matched to the cooling application’s specific horsepower, speed and torque requirements, allowing data center designers to optimize and reduce the supporting electrical infrastructure, while achieving performance targets to reduce energy consumption by 10-15%.
As data center cooling equipment manufacturers continue to innovate with more efficient HVAC designs, there are three main considerations for sustainable data center cooling that begin with the motor. Below, I’ll explain why each should be considered when introducing a motor into the data center environment:
High-Efficiency Levels Across a Wide Range
Traditional motors that feature an iron core with copper windings will often experience eddy currents that result in motor losses. Replacing the iron core and copper windings with a PCB stator eliminates these losses, resulting in a higher efficiency motor not just at the rated power and speed, but across the entire operating range (including partial load conditions). In motors that use PCB stators, copper can be etched directly into the PCB, which also increases the reliability and life of the stator, and significantly reduces the amount of copper material needed.
In a data center, where loads can vary widely depending on the time of day, it’s important to identify a motor that has a flat efficiency curve across a wide range of load conditions to optimize overall HVAC system efficiency and operations. Doing this will ensure the system will benefit from optimum efficiency under a variety of operating conditions.
Advanced air core motors that leverage PCB stators can run at variable speeds with partial load efficiency, saving energy at off peak times, while maintaining high levels of efficiency across a wide range of loads and speeds. For example, air core motors used together with an efficient fan can improve wire-to-air efficiency, and create a fan with a flat efficiency curve across full and partial load conditions.
Precise Controls and Intelligence
Improvements to motor efficiency and demand-based variable speed controls can save upwards of 65% of energy use depending on the application. Control capabilities for motors range from basic speed control options to more sophisticated speed control features and capabilities. Variable frequency drives (VFDs) that use silicon carbide can operate at higher switching frequencies and temperatures, with fewer losses, and can provide precise control in overall power and energy savings for the motor system.
Having more intelligence built into motors can also allow data centers to require fewer motors for redundancy on fan systems, while also running them at their most efficient operating speeds. Today’s motors can integrate MODBUS, BACnet and SCADA connectivity to communicate motor performance and health data back to a controller or centralized control system. IoT connectivity can also be used to monitor critical equipment to optimize building operations, and alert operators to high temperatures or other system parameters that are out of pattern or range so they can proactively address issues before something fails.
Sustainable Design
With data center space at a premium, design is an important consideration. Motors that take advantage of more compact, axial-flux designs and thin PCB stators (versus heavier iron-core motors) can result in 50% smaller and lighter form factors and reduce overall space required in data center air handling, chillers, coolers and liquid cooling applications.
This can allow for closer proximity to data center equipment and for more effective, efficient cooling and removal of heat. Smaller, lighter motors can also allow for ease of installation and make access easier for maintenance.
Sustainable design that minimizes the use of raw materials and incorporates end of life management can support initiatives to reduce waste. Today, the majority of motors end up in landfills after 10 to 20 years, but advances in circular motor design are allowing for extended component life and reuse. Data centers have hundreds to thousands of motors with valuable materials, such as aluminum, steel, magnets that can benefit from refurbishment and reuse, rather than being thrown into a landfill. Motors that take advantage of modular design can make the motor easy to maintain and allow for components to be reused multiple times.
In conclusion, responsible design in data center cooling equipment is increasingly becoming a priority as data centers continue to grow in number and energy usage. Advanced motors that operate with high efficiency across a wide range of speeds, have precise control and intelligence capabilities, and those that are built with sustainable design in mind can play a major role in reducing the carbon footprint of HVAC systems and data centers overall.