How the Smallest of Components in your Motor May Have the Largest Impact on its Life Expectancy: Understanding Bearing Basics
When we talk about motor systems, it’s not if the motor will fail, it’s when.
Bearings are one of the main failure modes on an electric motor. High-frequency harmonics induce unbalanced phase voltages and currents in the stator and rotor cores. Add in thermal considerations, and over time, bearing lubricant can’t stand up to those conditions, and the bearing fails. Understanding bearing specifications during the process of motor selection can be a critical element in the effort to optimize the lifetime expectancy of your motor.
Bearing Basics
Before diving into the nuances of bearing selection, it’s important to understand the basic components that make up the structure of bearings and how each element plays a role in performance.
-
- Rolling Elements: Balls and cylinders are the rolling elements in the bearing structure. While they can be made of plastic or ceramic, they’re typically made from high purity chrome alloy steel.
-
- Race: The inner and outer race are mostly made from high purity chrome alloy. The raceway transfers force radially and/or axially depending on orientation. For motor applications, the inner race is rotating with the shaft and the outer race is stationary; rotors are connected to the shaft and rotate at the same speed.
-
- Cage: Made from steel, brass, or polymer, the cage keeps rolling elements separate, so they don’t collide, while allowing them to rotate freely.
-
- Shield / Seal: This combination offers protection against outside debris and keeps grease in. The shield is typically a metal plate while the seal is Nitrile/BUNA-N (NBR) or Fluoro (FKM) rubber.
Overall, bearing configuration depends on the application area. For example, the purpose of the shield / seal configuration is to retain grease and keep out debris, but the consequence is higher bearing loss. In electric motors, that increases the likelihood of seal failure. However, in water-tight environments (e.g., IP55 against water jet), a sealed bearing is mandatory (if there are no external seals), so the engineering team has no choice but to cope with lower motor efficiency due to the bearing loss in that case.
L10 and L10g
At Infinitum, we get a lot of questions about bearings—usually in the form of L10 life. By definition, L10 life refers to the number of hours in service at which 10 percent of bearings will fail due to metal fatigue (i.e., 90 percent reliability). It’s a measure of physical component life, and, by extension, provides insights on maintenance; downtime contributes to loss of revenue and additional service costs.
Grease life, L10g life, acknowledges the complexity of grease lubrication mechanisms by using empirical models as a basis for calculation. High temperature dramatically impacts L10g life. In motor applications, hybrid bearings, with ceramic balls and steel races, run much cooler, so they approximately double L10g life values compared to a steel bearing.
In large motors (i.e., 100 to 500 horsepower and up), L10 life is the more important calculation to consider because there are no pre-packed grease bearings. Regular re-greasing is part of maintenance. For smaller motors, like those produced by Infinitum, L10 grease life is the most important determining factor from a maintenance standpoint because of those pre-packaged grease bearings. Typically, grease will deteriorate faster than the actual component.
That said, these values hold a lot less meaning without context. L10 and L10g life are predominantly based on the speed and orientation of the motor that was used for assessment. When comparing L10 and L10g life values between vendors, make sure you’re comparing them within the same environmental context, or you won’t have an accurate snapshot of performance.
Material Selection
Materials matter when it comes to the physical life of components. Unless otherwise specified, Infinitum motors use steel bearings (balls and race).
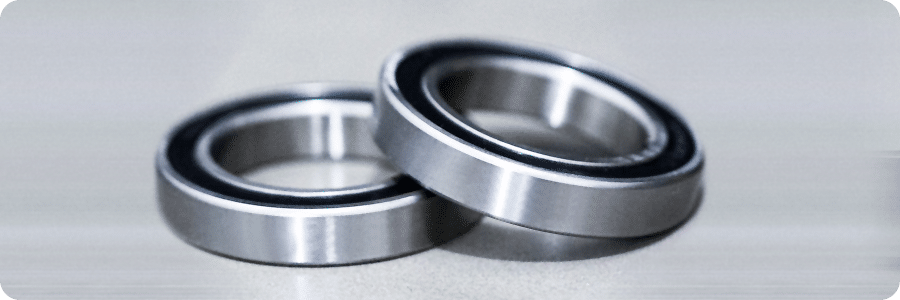
However, hybrid bearings (steel race, ceramic balls) balance performance and cost across a variety of motor applications. For instance, customers working in mission-critical applications where there are high temperatures, high speed, or strong electric current (e.g., data centers) tend to prefer hybrid bearings.
Infinitum uses hybrid 6200 series bearings or equivalent. Depending on the vendor, codes may provide more or less information about the bearing, but 6200 series specifications are consistent across the board.
There are certain situations where ceramic balls (i.e., silicon nitride) are better suited because they have stronger insulating protection than a steel balls. However, the price tag on hybrid bearings is 3 to 5 times higher than steel. Choosing to go that route adds additional safety margins to minimize risk, but it comes at a cost. On the other hand, applications with shock or sudden impact, like a monster truck motor, wouldn’t be ideal for ceramic balls because they’re too brittle to stand up to the shock.
Bearings play a critical role in motor design and operation. Understanding their characteristics provides helpful insights that set expectations for overall motor performance. At Infinitum, we look to understand your application and budget to ensure you have the best possible combination of components to keep your motor running. Contact us to discuss your upcoming project.
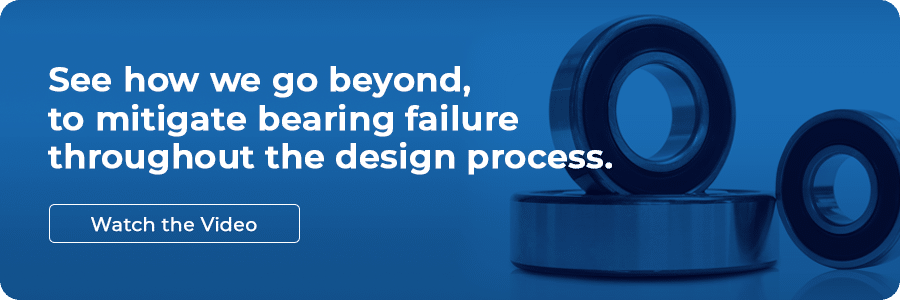