Two Distinct Realms for Electric Motor Reliability Optimization
Regardless of application, technical system performance and support costs depend on a motor’s ability to stand up to its environment. In a well-designed motor, reliability is essential. True, intrinsic reliability results from efforts in two distinct realms: motor architecture and predictive analytics.
From the motor architecture perspective, opportunities for reliability optimization appear in each major component of an electric motor. Condition of stator windings, sliding components, and bearings—the primary failure mechanism of an electric motor—all impact a motor’s lifespan:
- Stator Windings: The iron core and copper windings in a traditional motor have different thermal expansion coefficients from one another. By nature, they expand at different rates as motor temperature changes, causing cracks in the winding insulation. Infinitum’s approach to this problem involves a PCB stator with layers of copper and glass-epoxy laminate. With less a smaller discrepancy in thermal expansion coefficient, temperature changes cause uniform contraction and expansion that prevents thermal cracks.
- Bearings: Heat is a primary issue to contend with because it degrades bearing grease. System design should focus on keeping bearings cool and properly loaded. Exceeding a motor’s operational specifications shortens its life by adding unnecessary stress on the bearings. Early in development, Infinitum employs heat sink optimization and other thermal management techniques to achieve cooler operating temperatures for the whole motor.
Infinitum motors come standard with steel bearings (balls and race), but hybrid ceramic bearings (steel race, ceramic balls) are available upon request. All Infinitum motors have an L10 bearing life of 50,000 hours for all orientations.
For more information on motor architecture and predictive analytics in electric motor design and manufacturing, check out our white paper “Designing Electric Motors for Intrinsic Reliability” where we’ll cover:
- Areas of an electric motor that offer the greatest opportunities for design optimization
- How analytics can help mechanical engineers apply precision improvements for greater reliability
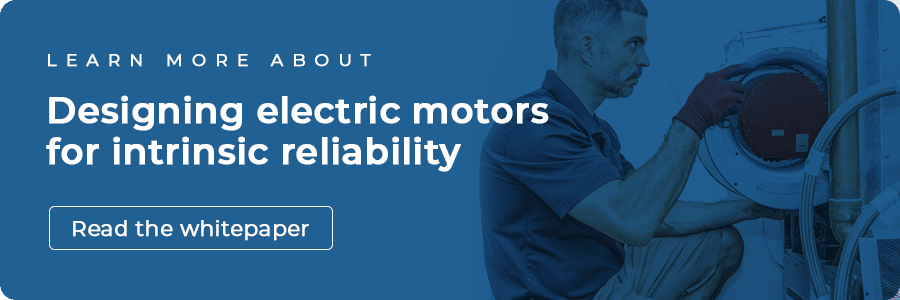