Start- and Scale-up of the Week: Infinitum
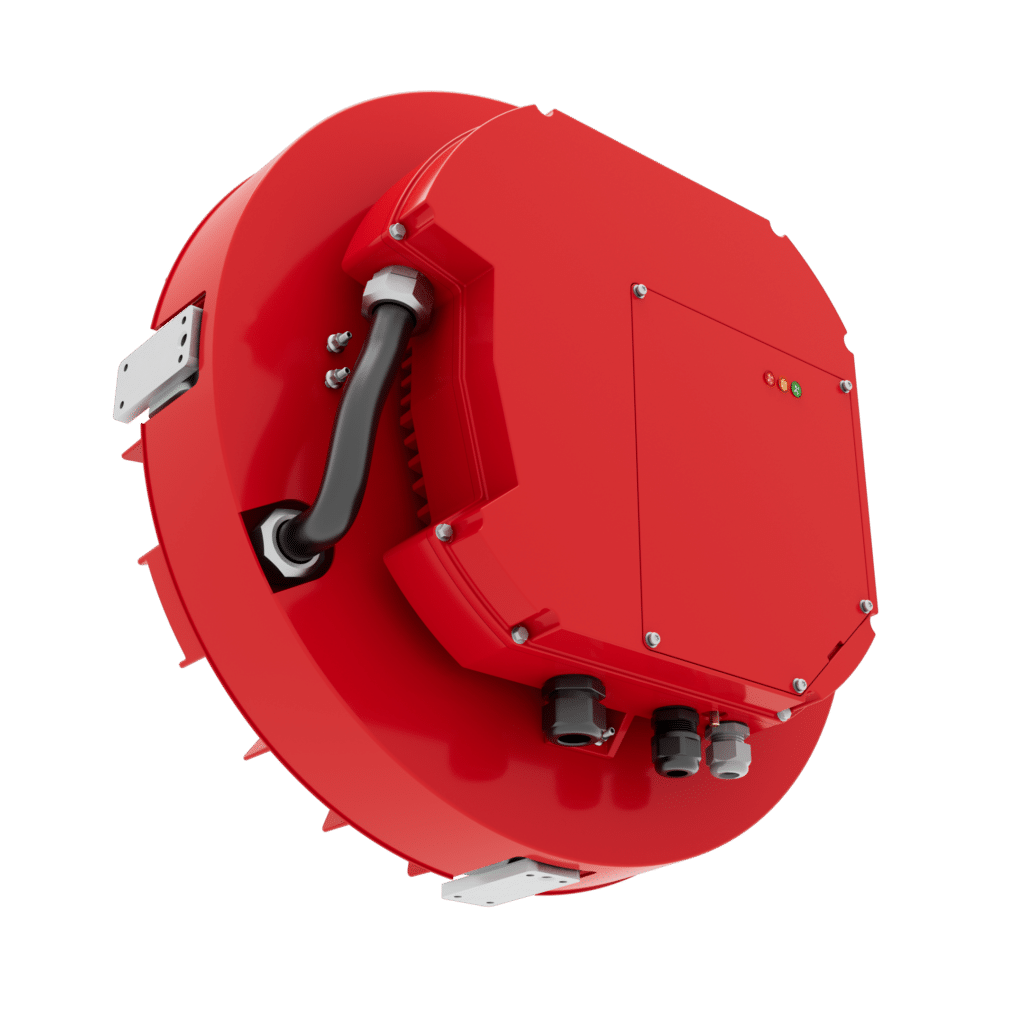
Infinitum’s latest generation Aircore EC motor system
Infinitum
Employees: 150
Funding round: $185m in Series E funding (announced Nov. 1)
Headquarters: Austin, Texas
Tell us about your company.
Infinitum is mitigating climate change with a next generation motor system that is better for the planet. The company’s electric air-core motor systems have raised the bar for sustainability and usability, offering a path to reduce global electricity demand and decarbonize some of the highest emitting and hardest-to-abate sectors, including commercial, industrial and transportation.
Designed with future generations in mind, Infinitum motors go beyond efficiency – taking the entire product lifecycle into account by using fewer resources to produce it, less energy to run it and a commitment to remanufacture it.
Infinitum’s electric motors open up sustainable design possibilities for the machines we rely on to be smaller, lighter and quieter, improving our quality of life while also saving energy and reducing waste. Based in Austin, Texas, Infinitum is led by a team of industry experts and pioneers.
Why is the technology your company works on important to the future?
The industrial manufacturing sector is shifting towards electrification and away from the fossil fuels previously used in high-heat processes, small industrial vehicles and in the heating of warehouse and manufacturing spaces.
As a result, electric motors are growing in number, driving power for forklifts and tugs, running generators and powering heating and cooling systems. By 2040, 30% of the growth in global electricity demand is expected to come from industrial motors as the sector expands and electrifies further.
Advanced motor technology, like that provided by Infinitum, offers higher efficiency and integrates variable frequency drives (VFDs), which permit the motor to adjust speed to meet the actual power demand of an application, and save energy. New modular designs also allow for easier serviceability to keep motors in service and out of landfills.
According to the U.S. Department of Energy, the implementation of advanced motor technology – such as Infinitum’s – in the US industrial and commercial sectors can save 127 terawatt-hours per year (TWh/yr), resulting in cost savings of $14.7 billion and reductions of 90.2 MMT of CO2. That’s equivalent to the annual electricity use of all households in California and North Carolina combined.
What makes your company’s approach unique?
Infinitum motor systems are designed with sustainability and circularity in mind. Infinitum motors replace the heavy iron core found in traditional stators with a lightweight, printed circuit board (PCB) stator that is 10x more reliable. Using a PCB means the motor can be smaller, lighter and quieter than motors that use conventional iron core stators. Infinitum also etches copper onto the PCB, which allows for a significant reduction in copper.
With 44 patents and 47 pending, Infinitum’s motor is 50 percent smaller and lighter, uses 66 percent less copper and no iron in the stator, and consumes 10 to 65 percent less energy than traditional motors.
Infinitum motors systems can also be tailored to fit specific application power, torque and input current requirements to save up front cost infrastructure costs as well as energy. This is more economical and sustainable for customers who previously had to use motors based on standard sizes that are less efficient for their particular application. Additional features, such as optional IoT capabilities and Infinitum’s I-con motor control software ensure continuous monitoring and reporting of carbon emissions, energy consumption, heat and vibration for optimal energy management, performance and predictive maintenance.
A majority of conventional motors are thrown into landfills at their end of life. Infinitum motors use fewer raw materials in manufacturing and modular design allows for motors to be easily serviced, repaired, remanufactured or recycled. When hundreds or thousands of motors are used in an industrial or manufacturing facility, reducing the energy demand, emissions and waste created by motors can make a sizable impact.
Anything else you’d like to add?
Rockwell Automation and Infinitum are jointly developing a motor system that is compatible with Rockwell’s industrial automation solutions. Rockwell’s PowerFlex® drive technology will be combined with Infinitum’s high-efficiency Aircore EC motor system. The joint solution will help companies reduce their carbon footprint with a motor system that is 50% smaller and lighter, uses 66% less copper, and consumes 10% less energy than traditional iron core motors. The resulting motor and low-voltage drive solution will be distributed through Rockwell, expanding the opportunity for global industrial sector clients to easily deploy a sustainable motor system and cut energy consumption, operating costs and material waste.