Seven Ways to Create Supply Chain Resilience in an Uncertain World
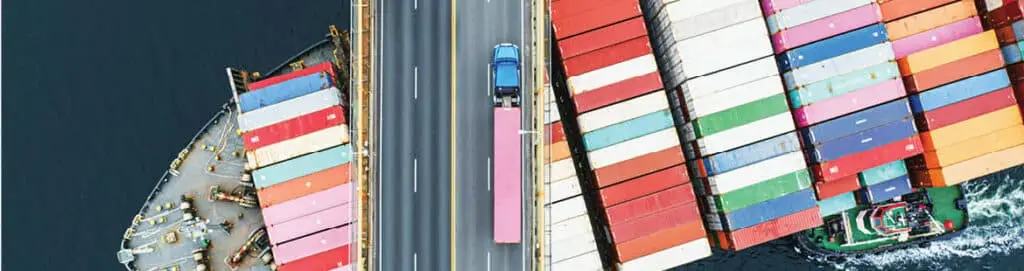
By Michael Gray, chief operating officer, Infinitum Electric
The COVID-19 pandemic sent shockwaves through supply chains around the world. Labor shortages, sourcing issues, and shipping delays revealed costly supply chain risks beyond our control. Now, two years after the start of the pandemic, organizations are still feeling its effects. Still, manufacturers have more options to build resilient supply chains for long-term viability.
Global supply chain disruptions cost large companies on average $184 million a year, according to the Interos Annual Global Supply Chain Report. In addition to the costs, 83 percent of respondents reported that their respective firms suffered reputational damage.
In the second quarter of 2020, McKinsey surveyed 60 senior supply-chain executives from across industries and geographies, asking them about the impact of the pandemic on their operations and their plans to make supply chains far more flexible and agile. The overwhelming majority of respondents (93 percent) planned to increase the level of resilience across their supply chain.
In our experience, developing next-generation motors, resilience has been important since day one. We believe it will continue to be critical for manufacturers building the next generation of products. While sourcing electronic components remains a challenge in this environment, the following considerations can help manufacturers design and deliver products with greater resilience.
Diversify Suppliers: Consider exploring different sources and locations for suppliers to avoid dependence on a single source. The goal should be to work with more than one country and more than one supplier for each part. In addition to expanding our sources, we’ve invested time with our suppliers to explore their flexibility in making additional parts or swapping parts that are similar in function and materials needed. When expanding and diversifying parts and sources, be open-minded to new possibilities and ideas. This concept of being more flexible to diverse sources also requires a company commitment and buy-in from engineering and across the organization.
Materials Makeover: Making products with fewer materials, or replacing harder-to-source components with off-the-shelf materials can make it easier and faster to manufacture products. Many of our components can be made without specialized equipment and require simple casting or machining processes. We have also reduced the number of materials needed to manufacture our motor. For example, we minimize the use of copper by replacing the heavy iron core found in traditional motors with a common, lightweight printed circuit board. Instead of winding copper around the heavy iron core by hand, we etch copper traces onto a printed circuit board. This approach allows us to make a motor using only a third of the copper used in a traditional motor. We also maximize our use of recycled magnets.
Make it Modular: The ability to assemble products on-site can speed time to delivery and reduce shipping and logistics costs. For example, our motor is designed using a modular architecture made of eight parts that allow for simple, Lego-block assembly on-site. Determine if product firmware can streamline product delivery. Our motors share common frame sizes, and tuning firmware architecture allows us to quickly customize and meet customer expectations. Our motor’s compact size also allows for twice as many motors to be shipped, which reduces transportation requirements, costs, and associated emissions.
Build Anywhere: The ability to build products in various locations and without specialized equipment or skills can significantly reduce the risk of supply chain vulnerabilities and shipping or logistics costs. For example, our motor replaces an iron core found in traditional motors with a printed circuit board (PCB). The PCB can be built in several regions globally, allowing us to localize production closer to where products are consumed, reducing lead times and shipping and logistics costs.
Commitments Count: When working with supply partners, booking production slots months in advance can reduce delays and ensure production happens as scheduled. Partners often appreciate longer-term commitments for their planning purposes, and it can, in turn, strengthen your position as a customer. If you’re a small company starting out, be sure to promote your product’s value and opportunity, explore suppliers that demonstrate support for newcomers, or programs that give guidance and support for emerging technology companies.
Consolidate Shipping: Consider and explore ways to consolidate or reduce shipping amongst different regions, suppliers and third-party logistics partners across the supply chain. This is a strategy that can reduce complexities, delays, and costs, while also benefiting your supply chain partners by simplifying their operations.
Foster Relationships: Treat your supply chain partners like you treat your customers by building long-term relationships that will benefit their business, not just yours. Maintain open, honest communication and get to know your partners on a personal level; acknowledge their successes, joys, and hardships. In a pinch, a solid partnership can help you both navigate and overcome a supply chain challenge or problem when you need it most.
As we continue to manufacture products in challenging environments, these seven considerations can help you build more resilience into your products and supply chains. In doing so, we will emerge stronger as we reimagine and adapt products for agility and resilience. ei