Printed Circuit Board Stator Maximizes Efficiency in Motor Applications
Infinitum Electric, a Texas-based company founded in 2016 with the mission to power the electric revolution, has patented a stator technology destined to change the electrification landscape, allowing for smarter, lighter and quieter electric motors and generators with unparalleled efficiency and durability.
Twenty-five trillion kilowatt hours of electricity are consumed per year, of which 53 percent is consumed by traditional electric motors. Maximizing efficiency, while reducing carbon footprint, is therefore a mandatory task.
“Being able to create incremental improvements in efficiency can have a dramatic impact on electricity consumption on a global level,” stated Ben Schuler, co-founder and CEO at Infinitum Electric in an interview with EE Times.
Infinitum Electric (IE) has developed an ultra-compact and highly efficient electric motor which achieves a weight reduction of up to 50%. The approach adopted to obtain a motor with lower weight and smaller size was to reduce the use of metals, transforming the classic stator into a real printed circuit board (PCB). This solution, in addition to allowing a saving of mass and dimensions, promises to reduce the use of copper and iron.
“We have eliminated all the external iron and copper windings present in the stator. The copper circuit is integrated into a single printed circuit board, thus reducing the energy losses associated with the core,” said Ben Schuler.
The Printed Circuit Board (PCB) stator, shown in Figure 1, also allows for mounting sensors and other electronic components directly on the same PCB, unlike traditional electric motors where additional components must be installed separately. The stator, integrating the entire coil, guarantees greater efficiency (at least 2% more efficient than a regular electric motor, which already has a 95% efficiency rate) and duration by virtue of a coefficient of thermal expansion that remains uniform in all points.
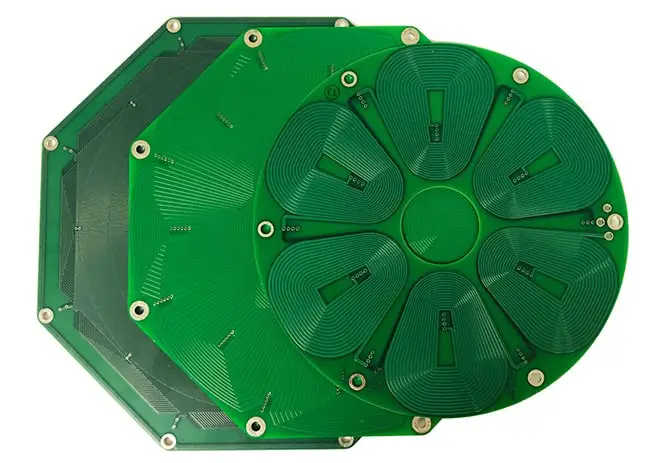
In addition to reducing the weight by 50% compared to a traditional solution, the IE Printed Circuit Board stator is able to eliminate torque ripple. This aspect is very important as it allows, in turn, to obtain quieter engines even when operated at low rpm. In addition, the Print Circuit Board drastically improves the insulation of the copper conductors, protecting them from potential short circuits or other faults. As if that were not enough, the Printed Circuit Board stator developed by IE is 15% cheaper and has no cogging torque, an aspect that allows for the extension of the drive system lifetime and reduces noise by up to 15 dB compared to an iron core motor.
A dedicated software application developed by Infinitum Electric, IE AutoFLUX, simplifies and accelerates the design and development phases of a new Printed Circuit Board motor. As a matter of fact, IE AutoFlux motor design software enables users to input application requirements (such as size, speed, power, performance, and cost), evaluate design options based on these requirements, and automatically generate Printed Circuit Board design files for production within few minutes.
IE Product Families
The Infinitum Electric product portfolio includes three device families:
- IEs, a general-purpose series which addresses applications such as fans, pumps, and compressors. This product line is available in the 5-15 horsepower (HP) range and delivers the market’s most comprehensive line of electric motors with class-leading efficiency and IoT capabilities in a package that is 50 percent lighter and smaller. Drastically reduced acoustic noise makes this the quietest motor system on the market
- IEm, the mobility series. When power density and performance matter most, the IEm series provides premium performance at a fraction of the physical weight. Removal of the conventional laminated stator core significantly reduces mass and the elimination of core losses improves efficiency to levels that are otherwise unobtainable. This product line applies to a variety of propulsion and auxiliary applications for automotive, aerospace, power sports and marine industries
- IEh, the consumer products series, intended for applications such as vacuums, dish-washers, and consumer appliances. The removal of the laminated stator core eliminates cogging and torque ripple which drastically reduces acoustic noise. Integrated electronics and embedded IoT circuity allow the motor to stay connected to the outside world
- IEx, the hazardous applications series. IE motors are designed to be compliant with Class 1/Div 1 and Class 1/Div 2 applications. The IEx Series is inherently spark proof and more cost effective than comparable hazardous rated products. The patented Printed Circuit Board stator produces perfectly symmetrical stator windings that are equally and fully insulated, resulting in higher reliability and longer lifetime. The IEx Series is applied in a variety of pump and blower applications for hydrogen, natural gas, petroleum, and chemical industries
- IEq, a smart motor platform with IoT and advanced drive features. The IEq platform is a visionary offering comprised of cutting-edge motor controllers, industry-leading communications options, and user-centric cloud capabilities.
The IEs Series motor product line has been recently expanded with new power and frame sizes to better address the requirements for fans, pumps, compressors, conveyors, and general-purpose applications (Figure 2). Infinitum Electric’s IEs Series product line is now available in the 5-15 horsepower (HP) range. By broadening the range of power beyond 7.5 and 10 HP, Infinitum Electric is delivering the market’s most comprehensive line of electric motors with class-leading efficiency and IoT capabilities in a package that is 50 percent lighter, smaller and significantly quieter than conventional motors.
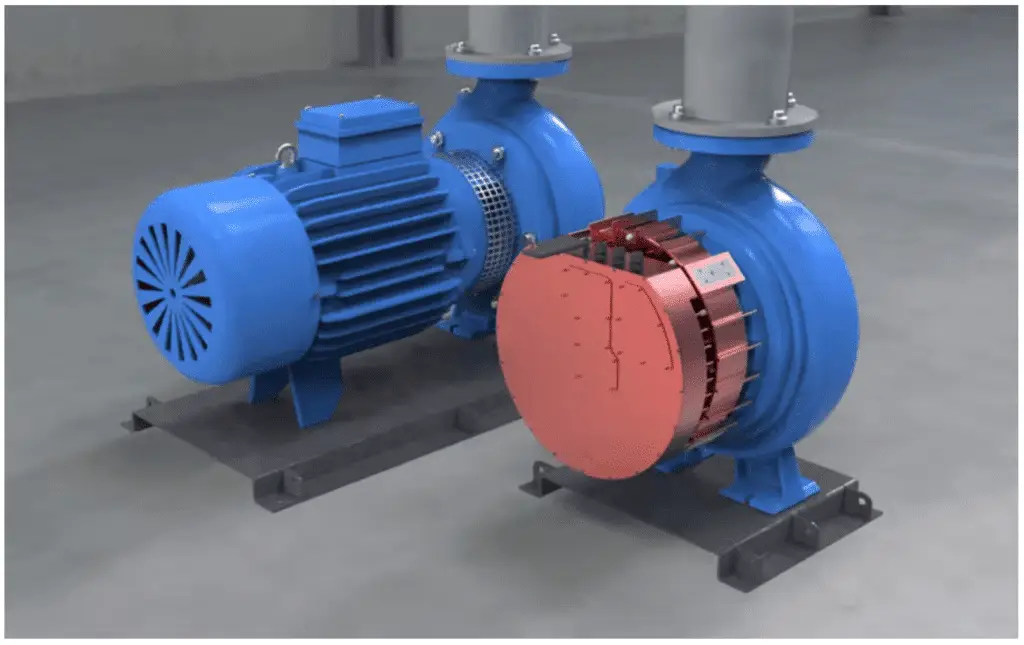
“Building on the success of our IEs Series for the HVAC industry’s leading manufacturers, we’re excited to drive innovation further with a compelling range of higher efficiency, lightweight motors,” said Ben Schuler, founder and chief executive officer, Infinitum Electric. “Extended power and frame options open design possibilities for a wider variety of use cases. Now fan and pump designers can take advantage of the IEs family’s low noise profile, lighter weight, smaller size and higher efficiency to differentiate even more of their next generation products.”
IEq motor controllers are variable speed drives that feature ultra-efficient silicon carbide (SiC) technology. The IEq controllers are physically integrated into IEs and IEx series motors resulting in a compact motor-drive package suitable for direct-drive applications.
“In order to support variable frequency drive (VFD) control, we have to drive the motor with a very high switching rate, and we have opted to use ultra-high efficiency silicon carbide devices able to switch at up to 200 kHz frequencies,” said Ben Schuler.
The integrated electronics and embedded IoT circuitry allow the motor to stay connected to the outside world, providing data collection and performance monitoring. The cloud platform provides real-time insights into motor performance and operation, enabling remote monitoring and over-the-air (OTA) firmware updates.