Infinitum Electric brings its PCB stator technology to EV motors
By Charles Morris & filed under Features, Tech Features
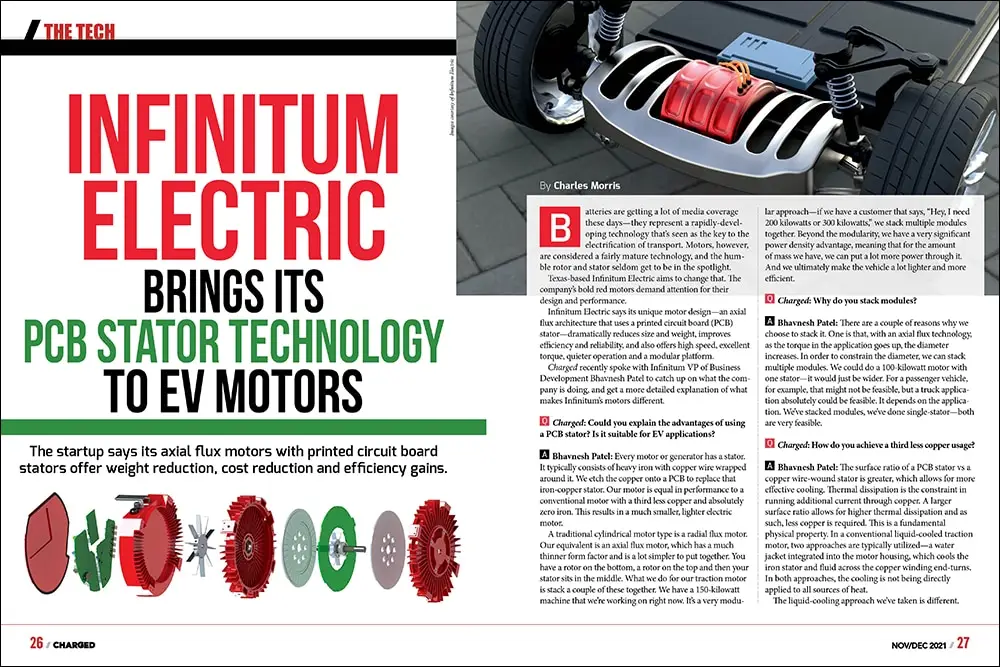
Infinitum Electric says its axial flux motors with printed circuit board stators offer weight reduction, cost reduction and efficiency gains.
Batteries are getting a lot of media coverage these days—they represent a rapidly-developing technology that’s seen as the key to the electrification of transport. Motors, however, are considered a fairly mature technology, and the humble rotor and stator seldom get to be in the spotlight.
Texas-based Infinitum Electric aims to change that. The company’s bold red motors demand attention for their design and performance.
Infinitum Electric says its unique motor design—an axial flux architecture that uses a printed circuit board (PCB) stator—dramatically reduces size and weight, improves efficiency and reliability, and also offers high speed, excellent torque, quieter operation and a modular platform.
Charged recently spoke with Infinitum VP of Business Development Bhavnesh Patel to catch up on what the company is doing, and get a more detailed explanation of what makes Infinitum’s motors different.
Charged: Could you explain the advantages of using a PCB stator? Is it suitable for EV applications?
Bhavnesh Patel: Every motor or generator has a stator. It typically consists of heavy iron with copper wire wrapped around it. We etch the copper onto a PCB to replace that iron-copper stator. Our motor is equal in performance to a conventional motor with a third less copper and absolutely zero iron. This results in a much smaller, lighter electric motor.
We etch the copper onto a PCB to replace that iron-copper stator.
A traditional cylindrical motor type is a radial flux motor. Our equivalent is an axial flux motor, which has a much thinner form factor and is a lot simpler to put together. You have a rotor on the bottom, a rotor on the top and then your stator sits in the middle. What we do for our traction motor is stack a couple of these together. We have a 150-kilowatt machine that we’re working on right now. It’s a very modular approach—if we have a customer that says, “Hey, I need 200 kilowatts or 300 kilowatts,” we stack multiple modules together. Beyond the modularity, we have a very significant power density advantage, meaning that for the amount of mass we have, we can put a lot more power through it. And we ultimately make the vehicle a lot lighter and more efficient.
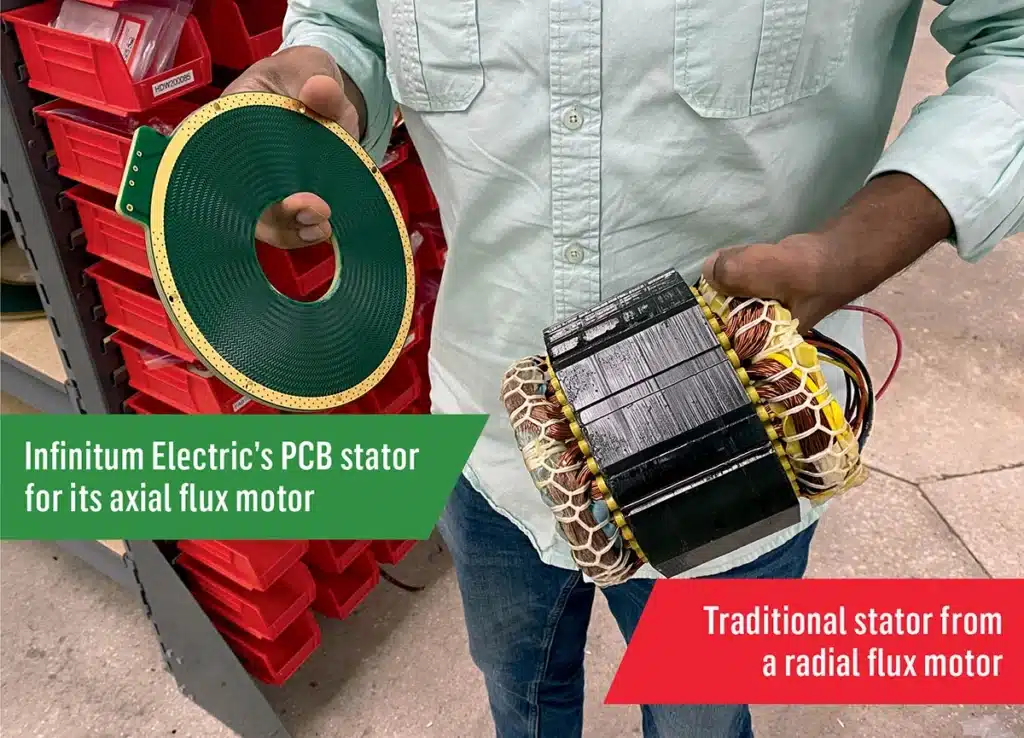
Charged: Why do you stack modules?
Bhavnesh Patel: There are a couple of reasons why we choose to stack it. One is that, with an axial flux technology, as the torque in the application goes up, the diameter increases. In order to constrain the diameter, we can stack multiple modules. We could do a 100-kilowatt motor with one stator—it would just be wider. For a passenger vehicle, for example, that might not be feasible, but a truck application absolutely could be feasible. It depends on the application. We’ve stacked modules, we’ve done single-stator—both are very feasible.
Charged: How do you achieve a third less copper usage?
Bhavnesh Patel: The surface ratio of a PCB stator vs a copper wire-wound stator is greater, which allows for more effective cooling. Thermal dissipation is the constraint in running additional current through copper. A larger surface ratio allows for higher thermal dissipation and as such, less copper is required. This is a fundamental physical property. In a conventional liquid-cooled traction motor, two approaches are typically utilized—a water jacket integrated into the motor housing, which cools the iron stator and fluid across the copper winding end-turns. In both approaches, the cooling is not being directly applied to all sources of heat.
The liquid-cooling approach we’ve taken is different. We essentially hollowed out the shaft on the motor and inserted nozzles that spray the fluid across the surface of the entire stator. We’re getting the fluid directly on the heat source, and can more effectively remove heat from the motor. One of the limitations in how much current you can run through a stator, whether it’s ours or anybody else’s, is how hot it gets. And because we’re more efficient at removing heat, we can run a lot more current through it. Typically, with an air-cooled radial flux motor, your current density is in the range of 3-4 amps per square millimeter (3,000 amps per square inch). With our liquid-cooled PCB stator, we can run 42-56 amps per square millimeter (27,000-36,000 amps per square inch), so it’s orders of magnitude greater.
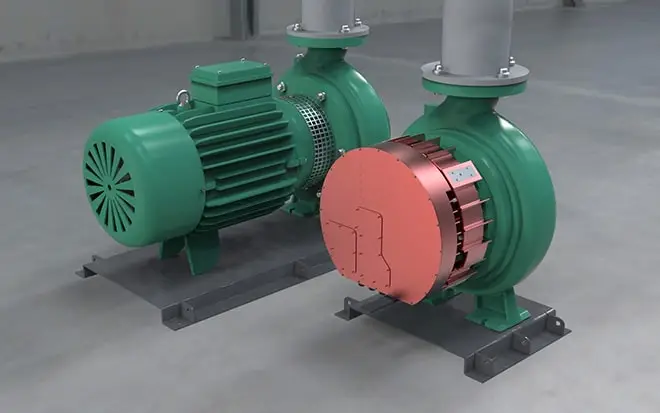
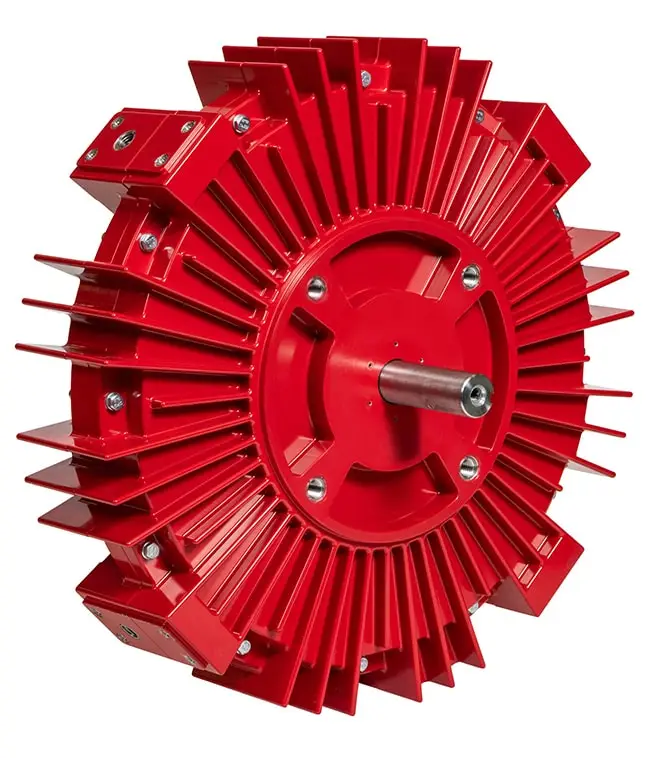
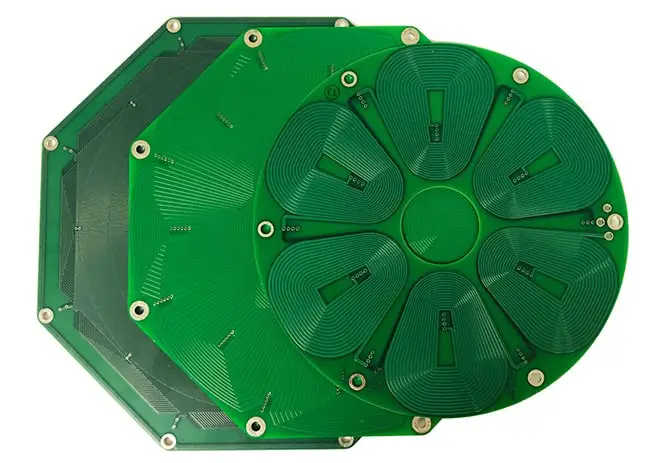
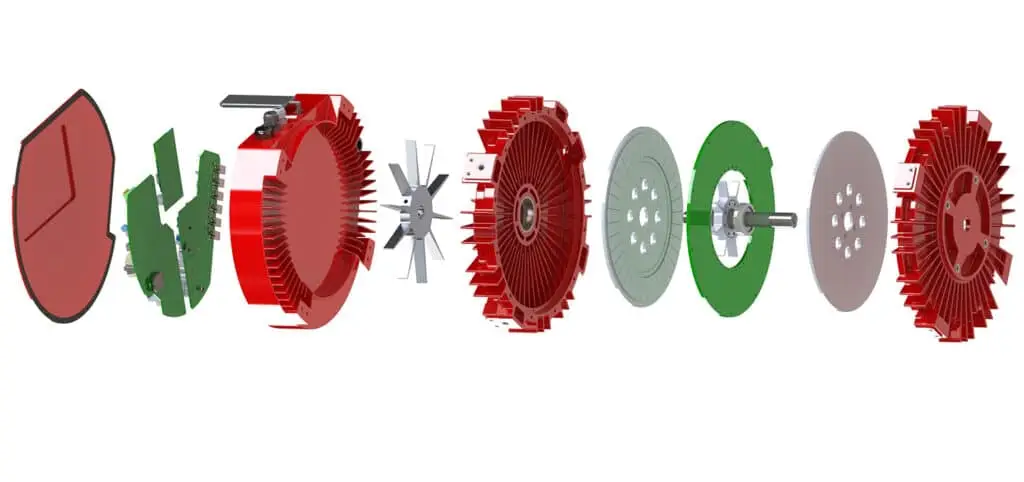
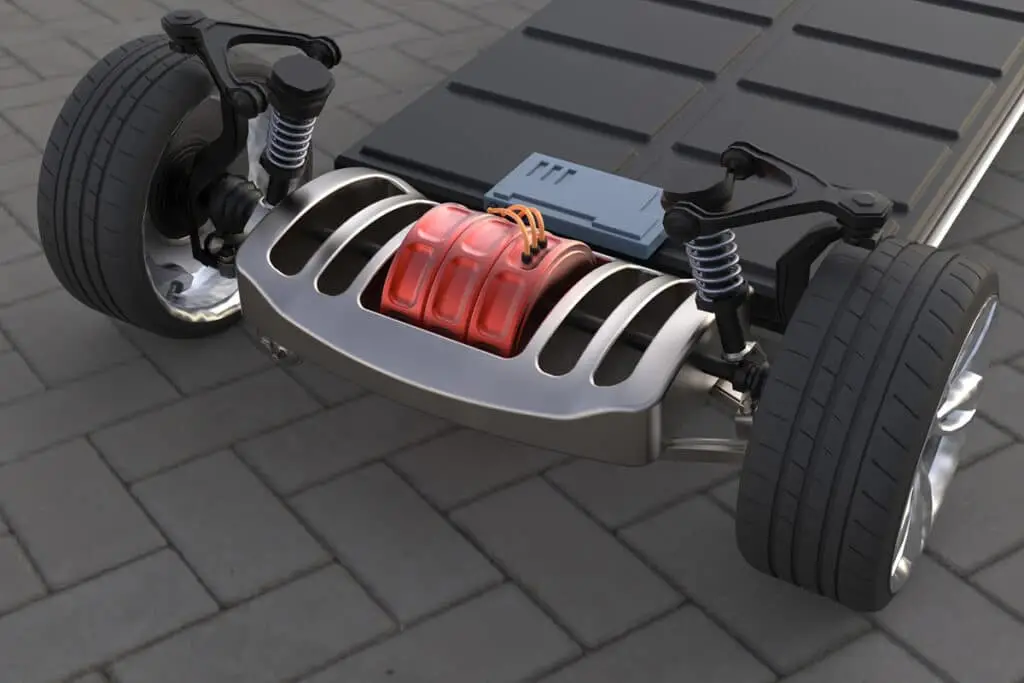
Charged: In the gap between the stator and the rotor, there’s a fluid?
Bhavnesh Patel: Yes. On a conventional radial flux motor, you have a very small air gap, and that air gap prevents you from having fluid on the inside of the motor because that fluid creates losses. With ours, we have a fairly wide air gap and in most cases, that wide air gap is a negative property. In our case, it enables us to run fluid without creating the losses you would typically experience with a radial flux motor.
Charged: Will it be completely filled with fluid?
Bhavnesh Patel: No, not quite. It will be sprayed with a relatively low flow rate. Most traction motors require a coolant flow rate in the range of 20 or 30 liters per minute. Our designs typically use a flow rate of 3 liters per minute. We’re simply spraying that fluid across the surface and don’t need as much liquid to cool the motor.
Charged: Do you have to coat the PCB with something special to keep it covered in fluid?
Bhavnesh Patel: No. In the first project we did with liquid-cooled motors we used DEXRON VI Automatic Transmission Fluid (ATF). We recognized it’s not optimized for cooling, but it’s a fluid commonly used as an automotive lubricant. We found that it really didn’t matter—having that fluid across the stator gave us very effective cooling. We didn’t make any modifications to the stator, so there was no special coating. More recently, we’ve worked with a couple of well-known chemical companies that have engineered more optimized fluids for electric motors. Those will improve thermal management even more than we’ve already achieved.
Charged: Is liquid cooling the big design challenge for EV applications?
Bhavnesh Patel: Yes. More generally, removing the heat from an electric motor is always a big concern. It doesn’t matter which traction motor you’re looking at—they all use liquid cooling to remove heat.
Charged: How does the efficiency of a PCB-stator motor compare to traditional iron cores?
Bhavnesh Patel: When you see an efficiency specification for any motor, it will typically list the peak efficiency, for example, 96%. We can match the peak efficiency of conventional iron-core motors, but more importantly, our part load efficiency, or the efficiency across the full operating range, is our competitive advantage. The efficiency of a motor is determined by variable and fixed losses. Variable losses fluctuate with the load and fixed losses are independent of the load. With conventional iron-core motors, both axial flux or radial flux, the iron core contributes to fixed magnetic core losses, which exist regardless of the speed or load. This results in a steep decline in motor efficiency as the speed and load are reduced. By eliminating the iron in our motor, we found that even at 30% load, we maintain very high efficiency. It’s not just the fact that we can match the peak efficiency target, we can also maintain a high level across a wide range on the speed/torque curve.
Charged: Your website says your motors produce very little noise because of the absence of certain magnetic forces between the rotor and the stator. Can you elaborate?
Bhavnesh Patel: When you have an iron core, there’s a magnetic interaction between the rotor and the iron. That magnetic interaction results in cogging torque, which is one of the sources of noise and vibration in an electric motor. Eliminating the iron eliminates cogging torque. The best way to think about it is, if you take a motor and you spin it with your hand, you can feel slight notching. With our motor, when you spin the shaft, it spins like a flywheel.
Charged: Are your motors in production for industrial applications?
Bhavnesh Patel: Absolutely. We’re in production. We got our first products UL-certified in 2021. We’re selling into industrial applications ranging from fans to pumps, and starting to enter material handling as well. That’s an Infinitum-branded product that we’re selling directly to companies making fans, pumps, conveyor systems, and other industrial applications. Caterpillar Venture Capital also recently invested in Infinitum Electric to develop a new line of smaller, lighter, quieter and more efficient alternators. Our alternators are expected to be one third the size and weight of traditional alternators. We’re targeting the growing $17-billion annual alternator market.
Being able to take what would typically be a 300-pound, couple-hundred-kilowatt alternator and make it a third the size and weight is very attractive, as it potentially reduces shipping and handling costs, material costs, and provides more efficient power generation.
Charged: So, would you say the main benefit to your customers would be weight reduction, and thereby cost reduction?
Bhavnesh Patel: Yes, weight reduction and cost reduction are key benefits, but I’d also add noise, vibration, reliability, and efficiency gains, which equates to extended vehicle range.
Charged: How does Infinitum Electric’s PCB design, prototyping and production process compare to traditional stator manufacturing methods?
Bhavnesh Patel: The process from idea to prototype and eventual commercialization is very different for our technology as compared to conventional motors. The first step is gathering basic application requirements, such as the power, speed, voltage, physical constraints, etc. We input these details into our automated design tool called AutoFlux, which produces dozens of options within minutes. Our electromagnetic engineers then filter out the most promising designs based on the client’s objectives (i.e. highest efficiency, lowest weight, or lowest cost). With input from our client, we’ll narrow down the list to a handful of promising designs and send the Gerber file to one of our PCB manufacturers (Gerber is the equivalent of CAD but for circuit design). Within a few days, we can have a new stator produced and ready for testing. The simplicity of the rest of our motor enables us to complete the prototyping and testing process in a fraction of the time.
Once prototyping is complete, serial production can be scaled up with limited capital investment. The PCB can be sourced from almost any region of the world, and the rest of the components require simple casting or machining processes.
Charged: Do you use the same magnet configurations as a standard axial flux motor, or is it something different?
Bhavnesh Patel: It’s a pretty standard magnet material and magnet configuration. The dimensions and the layout are fairly simple. There’s not a whole lot of complexity in terms of the shape of the magnets. If you look at some of the well-known EV manufacturers out there that use magnets in their motors, it’s a fairly complex geometry and a fairly complex process of placing those magnets into the rotor. Our approach is very simple. We have an automated machine that essentially slots magnets onto the rotor, and that’s it.
The coefficient of expansion of the FR4 and the copper are almost equal, so the whole board expands and contracts at an equal rate, and you never ever have wires rubbing against each other.
Charged: One of the failure points of a standard motor is that the insulation and the windings will break down. Tell me a bit about the insulation of your stators.
Bhavnesh Patel: You’re exactly right—one of the failure modes on a traditional motor is the copper wire windings eventually failing. On wound stators, you’re taking copper wire, you’re bending it over and over, then you’re running current through that, so you’re heating it up and cooling it down over and over again. Over time with expansion and contraction, these wires rub against each other and they eventually break. The other source of failure is the insulation which sits between the copper windings and iron. The copper and iron have slightly different expansion rates, which causes the insulation to fail over time.
The variability in the conventional stator manufacturing process introduces hotspots that create additional potential failure points. Our PCB stators, on the other hand, are made on a fully automated piece of equipment. You don’t have any of that variability that you typically see on an iron-core stator. As the stator heats up and cools down, the coefficient of expansion of the FR4 [laminate material used to make PCBs] and the copper are almost equal, so the whole board expands and contracts at an equal rate, and you never ever have wires rubbing against each other. There’s no possibility of that happening because of the way the windings are laid out.
We’ve eliminated two of the most common sources of failure. The next most common source of failure is the bearings. Any time you have an inverter-driven motor, it generates bearing currents, and these currents cause the bearings to prematurely fail. Motors typically use more costly ceramic bearings, or they have these grounding rings to mitigate this issue.
Charged: What about the standard lifetime of the PCBs? What fails on them if they do fail?
Bhavnesh Patel: There was extensive testing done on a three-megawatt motor for a wind turbine application, and they found that the PCB stator was about nine times more reliable than a conventional iron-core stator.
The main failure points are typically manufacturing defects. In some cases on any PCB production line, you might get voids in the board. The other possibility is vias, which are the interconnects between the layers, failing. The good thing is that all of those issues tend to be identified during the production process because there’s automated inspection equipment that can identify those defects prior to full production being completed. And PCBs have been around for a long time, so the process of quality assurance is robust.
Charged: Is there anything else on the circuit board? Do you have sensors and other circuits in there?
Bhavnesh Patel: Yeah, absolutely. Because we’re using the circuit board, it’s a lot easier to embed chips and sensors. We typically embed a temperature sensor and an accelerometer on the stator, so we’re able to detect the vibration and temperature of the interior of the motor. This allows us to determine the health of the motor, and also the driven equipment. For example, in a pump application, if you have a blockage in the pump, you might see that on the vibration of the accelerometer before you actually see that physically. In relation to EVs, you might see unusual operating vibration on your motor before you would actually see it in a real-life catastrophic failure.
Charged: Do you develop the power electronics as well?
Bhavnesh Patel:Yes, we’ve developed power electronics, both IGBT and silicon carbide MOSFET-based. We generally prefer the silicon carbide—it’s more efficient—so that’s generally been what we’ve led with, both on the industrial side and the EV side. Some of the partners we’re working with within the transportation segment have their own power electronic platforms that they prefer to use. We’re amenable to using their platform if they want, but we have our own as well.