How manufacturing experts are utilizing VFD and VSDs in their facility
Variable frequency drives (VFDs) and variable speed drives (VSDs) play a critical role in manufacturing facilities and they are being used in more diverse ways than ever. Learn how from several experts.
By Plant Engineering
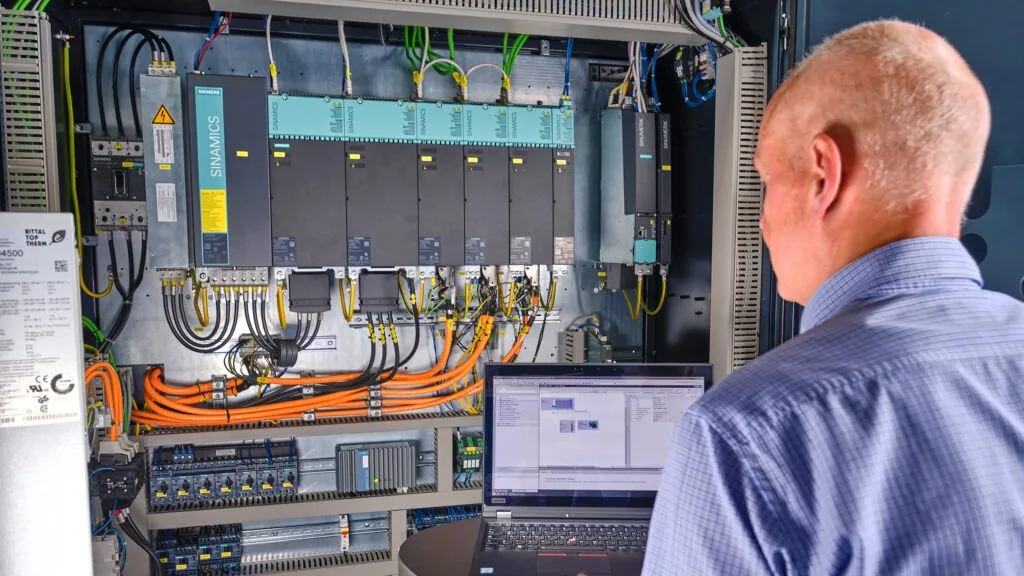
Decentralized VFD mounted next to motor. Respondents:
- Richard Barrows, senior electrical engineer, Hitachi Global Air Power, Michigan City, Indiana
- Zack Fowler, product marketing manager, Atlas Copco, Rock Hill, South Carolina
- Eder Matias, director of sales, drives, controls & automation, SEW-EURODRIVE USA, Lyman, South Carolina
- Craig Nelson, senior product manager, Siemens Digital Industries, Alpharetta, Georgia
- Paulo Guedes Pinto, chief technology officer, infinitum, Round Rock, Texas
- Brandon Teachman, owner, Automation Coffee Break, Appleton, Wisconsin
Question:
What are some of the current trends for variable frequency drives and variable speed drives (VFDs and VSDs) for industrial and manufacturing facilities?
Richard Barrows: Energy savings are key to their growth. Depending on the application, VFDs offer flexibility. They can turn off and on to tailor the air power output to your needs at the time.
Eder Matias: Rather than looking at specific VFD types, customers are looking for a VFD platform. This means creating products made to work together and are powerful and versatile enough to solve simple and complex applications without spending lots of money in trainings and costly support fees.
Craig Nelson: To save energy, space and costs, many VFD systems on production machinery are utilizing a common dc bus design. This configuration allows for regenerative energy from decelerating drives to be captured and used to drive other motoring loads. The elimination of a braking resistor to dissipate this energy into wasted heat energy adds to its growing popularity.
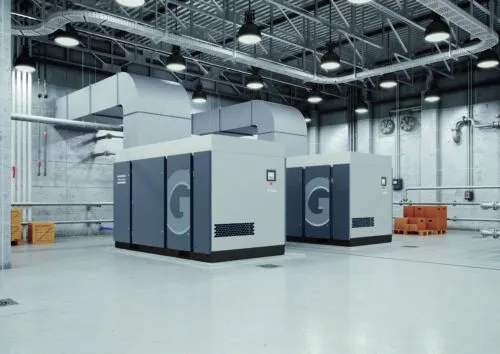
Atlas Copco’s GA VSD product line brings energy efficiency and reliability for industries worldwide. Courtesy: Atlas Copco
Paulo Guedes Pinto: From an application perspective, VFDs are being packaged into IP54+ enclosures and being placed closer to the motor. This avoids the need for space within the electrical cabinet for the VFD and makes maintenance easier. Also related to this trend is the use of quick disconnect cabling, which further allows for fast installation and easier serviceability.
The use of wide-bandgap technologies like gallium nitride (GaN) and silicon carbide (SiC) MOSFETs in consumer electronics, electric vehicles (EVs) and alternative energy inverters (solar & wind) has brought down costs making it more feasible to deploy into industrial VFDs. The benefit of utilizing GaN and SiC MOSFETS in VFDs as compared to traditional IGBTs include improved efficiency, smaller form factor and better thermal management.
Brandon Teachman: Trends in drive technology include reducing heat and putting the drive on a network. Conventional panel-mounted drives can shorten drive life due to heat. Flange-mounted or NEMA-rated drives dissipate heat directly into the environment, reducing energy losses. It is ideal for heat dissipation or space constraints. Drives can process, and the network enables the sending of motor performance data, analytics, and some amount of predictive maintenance. This also allows diagnostics and monitoring for troubleshooting issues remotely.
Question:
What long-term trends do you see for VFDs and VSDs (looking ahead to the next 12 to 18 months)?
Richard Barrows: The market is moving toward using permanent magnet motors to further drive efficiency. These are more efficient than traditional induction motors. They are becoming standard, and they require VFDs in order to operate.
Zack Fowler: One of the long-term trends we have noticed is to move from asynchronous motor to permanent magnet motor.
Eder Matias: It will be a combination of new technology and how it gets implemented. Energy management and storage combined with motion controllers, advanced decentralized VFDs and predictive maintenance are the next areas of industry focus.
Craig Nelson: Utilizing drive-based safety integrated functions has been a growing trend for years but now more advanced SI functions such as safe limited speed and safe operating stop are being incorporated into new innovative machine safety designs. The secondary effect of utilizing more safety functions in the VFD is the safety signals are migrating from HW safety inputs to a safety channel on the communications network.
Paulo Guedes Pinto: We see the adoption of IP54+ packaging and the use of GaN and SiC continuing to increase over the next 12 to 18 months. In addition, given the reduction in cost of power electronics, we see increasing adoption of active front end (AFE) enabled VFDs. AFE VFDs can provide regeneration, saving money and energy in some applications and reduced total harmonic distortion (THDi).
Question:
What are the primary advantages of using VFDs in motor control applications compared to other methods, such as soft starters or direct-on-line starting?
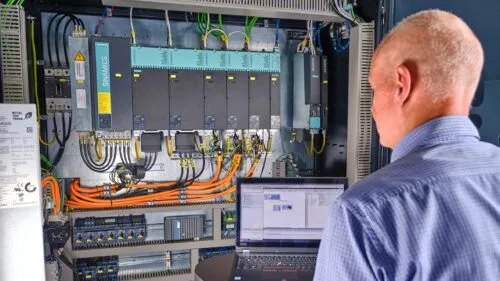
Decentralized VFD mounted next to motor. Courtesy: Siemens
Zack Fowler: VFDs significantly enhance efficiency, resulting in reductions in power consumption. They provide precise control over motor speed and torque, leading to smoother operations and extended equipment life.
Eder Matias: There are several advantages ranging from energy usage to ease of maintenance. In addition, despite all of the technical advantages, customers benefit by having a more flexible system which can easily adapt to different demands rather than running at a constant speed.
Paulo Guedes Pinto: There are several benefits to using a VFD compared to other methods, including energy savings, improved speed or position control, reduced starting current, integration with the control system, and built-in protection.
For centrifugal fan and pump loads, reducing the speed to 80% results in roughly 50% reduction in energy consumption.
In industrial applications such as cranes, elevators and material handling, the operator needs speed and position control. Older methods like soft-starts or direct-on-line starting do not offer this capability.
Brandon Teachman: VFDs are unique in motor control applications because they can regulate both motor speed and torque. Smooth acceleration and deceleration are possible with VFDs because they provide exact control over motor activities, in contrast to soft starters or direct-on-line starting techniques.
This flexibility is essential to ensure maximum performance and energy efficiency in applications where load circumstances change. Additionally, it enables you to adapt to changes in the mechanical components or process.
Question:
How do you select the appropriate size and rating of a VFD and VSD for a specific motor application? What are the key factors that need to be considered in this process?
Zack Fowler: By knowing the air demand of the customer application and operating pressure while considering pressure drops. Acknowledging the air purity requirements to provide a suitable solution. If they plan to expand its best to offer multiple machines with the VSD as the lead. If it’s a VSD and fixed speed combination, the VSD should be double the fixed speed.
Eder Matias: Several factors to consider are: Environment conditions, motor type, application, safety requirements, panel-mounted, motor-mounted or decentralized, communication with upper-level programmable logic controllers (PLC) or discrete input/outputs (I/Os). Customers also should consider a VFD platform which offers flexibility, regardless of the key factors being considered.
Paulo Guedes Pinto: Infinitum sells a combined motor and VFD system that avoids the need to select the components individually. In traditional applications where these components are sold separately, there’s several factors a user must consider including the motor requirements and load characteristics. The application’s load characteristics are crucial to understand in selecting a VFD to avoid field issues.
Brandon Teachman: There are few key pieces of information to consider:
- Know your motor: You will want all the information from the nameplate, but the essential item is the motor’s full load amps (FLA).
- What is the application? Some applications need the motor to run at a continuously high amp draw. In this case, most manufacturers will have you increase the drive size. Some applications, like a loaded conveyor, will have a higher FLA till they get to speed.
- Where is the VFD being placed? This includes the temperature range and enclosure rating (water, dust, etc.). The temperature range can affect the drive sizing.
Question:
As VFDs become more widely used in industrial and commercial settings, how do you ensure the compatibility and integration of VFD systems with other control and automation technologies?
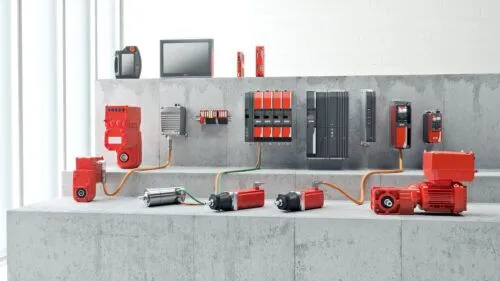
The MOVI-C automation platform is part of SEW-EURODRIVE’s Industry 4.0 approach and includes VFDs, HMIs, motion controllers, gearboxes, motors, servomotors and encoders, which are designed to work together seamlessly. Courtesy: SEW-EURODRIVE
Zack Fowler: Ensuring compatibility and seamless integration of VFD systems with other control and automation technologies is achieved through the use of OPC-UA. This communication protocol provides a reliable and secure framework for data exchange, enabling interoperability among various devices and systems, which is essential for modern industrial and commercial applications.
Eder Matias: Compatibility is a factor which should be considered early in the selection process. Selecting a manufacturer that offers motors, servos, gearboxes and drives with standard fieldbus communication eliminates the guess work and ensures compatibility among these components.
Paulo Guedes Pinto: The use of and adherence to industry standards is critical to interoperability, especially with regard to communication protocols like Ethernet/IP. Some standards, such as Modbus RTU, allow for a lot of interpretation, which occasionally creates issues between vendors.
Brandon Teachman: For a new application, I recommend that the person choses a drive with EtherNet/IP and write their program using the ODVA communication standard. This allows you to switch out a drive with multiple manufacturers. EtherNet/IP and ODVA are supported by many VFD manufacturers, allowing the end user to prevent supply issues.
Question:
With the rise of the Internet of Things (IoT) and Industry 4.0, how do you envision VFDs evolving to become smarter and more interconnected within larger control and monitoring systems?
Zack Fowler: With larger control and monitoring you will have better access to equalize running hours, narrowing pressure bands, more reactiveness to breakdowns which will improve productivity, efficiency and sustainability of products.
Eder Matias: Industrial Internet of Things (IIoT) is already a reality at SEW-EURODRIVE. Our MOVI-C automation platform is part of our Industry 4.0 approach and includes VFDs, HMIs, motion controllers, gearboxes, motors, servomotors and encoders — all designed to work together seamlessly. Thanks to our single cable technology, MOVILINK DDI, our VFDs enable asset management, motor temperature monitoring, vibration, brake pad wear and can warn the customer before a major failure happens.
Craig Nelson: VFDs are becoming a producer of data giving us insights into our equipment efficiency and mechanical condition. Feeding the motor operating conditions continuously back to edge or cloud platforms for analyzing gives us insight into any anomalies that can result in future downtime way before they happen. Further insights also tell us what can be improved or rightsized in the future.
Paulo Guedes Pinto: VFDs, like most devices at work and at home, are becoming smarter with increasing intelligence and capabilities. I envision VFDs interpreting application and on-device data to provide users with insights into the health of the asset. Over the past few years, this data has typically been pushed to an on-site edge or off-site cloud server for further analysis. With devices gaining more intelligence, this data could be processed and acted on locally.
Brandon Teachman: I believe VFDs will have the ability to pair with motor sensors directly. This would reduce the hardware needed to implement projects and allow you to get more predictive maintenance of the motor and drive, allowing users to increase the time of their lines.
I also believe that VFDs will add native message queuing telemetry transport (MQTT) Sparkplug B support. This allows for common communication between devices, PLCs, and software. Some VFDs have added MQTT support, but I believe Sparkplug B will become the standard.
Question:
What impact will the semiconductor industry have on the VFD market and manufacturing, both short- and long-term?
Richard Barrows: Supply for semiconductors seems to have leveled off from the shortages caused by the COVID-19 pandemic. At the same time, some chips are becoming obsolete, and must be replaced by readily available chips.
Zack Fowler: The semiconductor industry will have a significant impact on the VFD market and manufacturing in both the short- and long-term. As VFDs rely heavily on electronic chips and components in our drives.
Eder Matias: Semiconductors are the core of any industrial power electronics device. As the semiconductor technology evolves, VFDs are becoming smaller and offering higher overload capabilities. However, VFD manufacturers are vulnerable to changes or disruptions in the semiconductor industry. Companies which have learned from the semiconductors shortages will be better prepared for the future.
Read the full article at Plant Engineering