Identifying Opportunities for
Electrification in Industry
Electric motors are the world’s single largest consumer of electricity – we’re talking 53 percent of global consumption. But here’s the kicker: Only 20 percent of industrial energy consumption is covered by electricity. The rest is directly or indirectly powered by fossil fuels.
But that’s changing.
By 2040, 30 percent of the growth in electricity demand is expected to come from industrial motors. It’s a critical time for the industry sector. No single sector has more agency to reduce its energy footprint with commitment to efficient electrification of motors and other industrial equipment.
In 2021, the National Electrical Manufacturers Association (NEMA) launched the “Beyond Efficiency” initiative to emphasize that efficiency is table stakes for industry now. It’s not a feature anymore. As we work to design the next generation of motors, our mission is to build something that’s better for the planet and for all of us.
At Infinitum, we set out to design a motor that’s smaller, lighter, and quieter than a conventional motor, so we can be part of a radically sustainable future. If we all do our part, by 2040, there will be many companies across the industry in lock step with our mission.
Three Opportunity Areas for Electrification
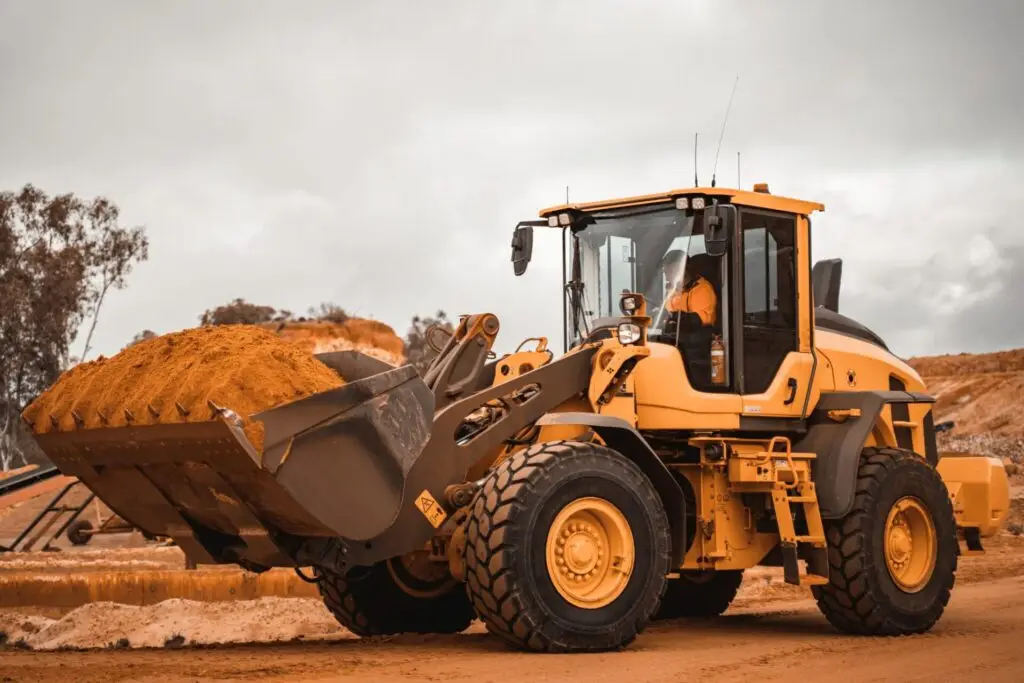
With Environmental, Social, and Governance (ESG) initiatives, shifting policy guidelines, growing customer demand, and a better outlook for operating costs, there’s an increasing number of incentives for industry stakeholders to lower carbon emissions.
Electrification can take different forms depending on the industry application area. The most common opportunities are (1) improving existing electric motors by replacing less efficient models with smaller, smarter, and more efficient ones or (2) fully replacing equipment that’s powered by fossil fuel sources with equipment powered by electricity. Here are a few industry areas that are ripe for electrification:
Fleets / Heavy Vehicle Equipment Applications
Think about how many fleets are involved in keeping our day-to-day lives running – cars, semi-trucks, passenger vans, etc. Today, regulations are beginning to force commercial fleets to go electric. According to a recent survey, industrial manufacturers have targets of almost 40 percent fleet electrification by 2035; fleets encompass anything from in-town delivery trucks to forklifts, so there’s a lot of potential for efficiency gains. Electric equipment in this area is typically cheaper to maintain and operate.
Further, we’re seeing a push for electrification in the heavy vehicles space. For example, a leading tractor manufacturer has approached Infinitum with the goal of transitioning from hydraulic to electric auxiliary motors. Older hydraulic designs still dominate in equipment like backhoes and bulldozers. Switching to electric auxiliary motors allows manufacturers to maintain the power needed for actuation and traction with a more efficient, environmentally friendly source.
Caterpillar and Rockwell Automation, both major players in the industrial sector, are Infinitum Electric investors. These companies see the potential for electric motors in the areas of manufacturing, materials handling, and power generation. There’s a great deal of equipment that keeps large-scale industry running, and it will run a lot more efficiently on electric.
Large-Scale Industry Processes
Many industrial applications make use of steam reform, drying, evaporation, distillation, activation, washing, rinsing, and food preparation processes to keep up with the pace of production. Today, most of these processes use fossil fuels directly (e.g., heat supply) or indirectly (e.g., utility systems).
But change is coming. Many manufacturers are looking to electrify nearly 45 percent of their processes by 2035. Given their superior design, relative to other options on the market, electric systems offer greater controllability and flexibility. These kinds of improvements lead to better lifetime performance. Considering that industrial processes lay the foundation for large-scale manufacturing, they’re a major target for electrification. The National Renewable Energy Laboratory (NREL) sees a lot of potential for technologies with high productivity benefits. With high adoption, 63 percent of curing needs, 32 percent of drying services, and 56 percent of other process heating could be electrified by 2050.
Industrial Spaces
Heat pumps present notable benefits for industrial settings. Typically, HVAC cooling and heating systems hum in the background largely unnoticed by building occupants, but electrification of these systems introduces the possibility for radically efficient building management. The market for heat pumps is expected to reach $9.87 billion by 2026. That’s not surprising. Heat pumps deliver about three units of heat for one unit of energy (generated from ambient heat). By comparison, a gas boiler delivers only about 0.9 units for that same one unit of energy.
While the initial equipment cost for electric heat pumps is typically higher than conventional gas-powered equipment, they can provide significant efficiency gains over a more conventional option. Electrical heat pumps can operate flexibly to balance the residual load in times of renewable energy production surplus.
Given their low utilization, office spaces, compared to other industrial spaces like factories and warehouses, are considered particularly wasteful. Today, about 40 percent of space and water is heated by electric, and the expectation is to see that move to 50 percent by 2035. Using occupancy sensors, smart building systems can provide additional energy savings that add up to big savings over time.
The Role of Ultra High Efficiency Motors in Industry
Most motors operating in industry today are not designed for variable speed operation or energy savings in general. The new generation of electric motor technology is getting smarter. More and more often, these motors feature a variable speed drive to boost energy efficiency and energy savings using more precise speed adjustments. For example, variable speed motors allow HVAC systems to adapt airflow for the realities of variable demand. In the off-hours, the system moves air at a lower volume (and lower energy usage) when there’s nobody occupying the space.
Motors, like those from Infinitum, are making their way into industrial spaces and applications. Manufacturers are starting to see the benefits of lower energy consumption, smaller form factor, and less noise in their own facilities and operations. Energy savings, and ultimately cost savings, foster even more support for industry-focused sustainability objectives.
For more information on the electrification of industry, check out The New York Times’ piece, “The Sustainable Industrial Revolution Is Just Getting Started,” featuring Infinitum founder and chief executive, Ben Schuler.